Introduction
In many industrial and daily – life processes, the formation of foam can be a troublesome issue. Foam is a dispersion of gas in a liquid, which is stabilized by surface – active substances. Excessive foam can lead to problems such as reduced production efficiency, inaccurate metering, and even equipment damage. Defoamers, also known as anti – foam agents, are substances specifically designed to combat this foam problem. They play a crucial role in a wide range of industries, from food and beverage to chemical manufacturing.
Working Principles of Defoamers
- Surface Tension Reduction
-
- Defoamers work mainly by reducing the surface tension of the liquid film that forms the foam bubbles. When a defoamer is added to a foaming system, it spreads quickly on the surface of the foam film. Most defoamers are composed of substances with low surface tension, such as silicone – based compounds or fatty alcohols. By spreading on the foam film, they disrupt the balance of surface forces. For example, in a water – based foaming system, the surface – active agents that stabilize the foam create a relatively high surface tension. The defoamer, with its lower surface tension, inserts itself into the foam film, causing the film to become thinner and less stable.
- Film Rupture
-
- Another mechanism is film rupture. Defoamers can penetrate the foam film and cause local thinning. Once the film becomes too thin, it ruptures, and the gas inside the foam bubble escapes. This is similar to how a small hole in a balloon causes it to deflate. The defoamer particles act as “weak points” in the foam film structure. For instance, solid – particle – containing defoamers can pierce the foam film, leading to its collapse.
Types of Defoamers
- Silicone Defoamers
-
- Silicone – based defoamers are one of the most widely used types. They offer excellent defoaming performance in a variety of systems. Silicone oils, such as polydimethylsiloxane (PDMS), are the main active ingredients. These oils have a low surface tension and high spreading ability. They can quickly spread on the foam surface and break the foam structure. Silicone defoamers are suitable for high – temperature applications, as they maintain their stability and defoaming efficiency even at elevated temperatures. For example, in the production of synthetic resins, where the reaction temperature can be quite high, silicone defoamers are often used to control foam formation.
- Mineral Oil Defoamers
-
- Mineral oil defoamers are composed of refined mineral oils along with additives. The mineral oil acts as the carrier for the defoaming components. These defoamers are relatively cost – effective and are commonly used in applications where cost is a significant factor. They are effective in many water – based systems, such as in the formulation of paints and coatings. The additives in mineral oil defoamers help to enhance their spreading and defoaming properties.
- Polyether Defoamers
-
- Polyether defoamers are based on polyether compounds. They have good solubility in some polar solvents and can be tailored to have specific properties depending on their chemical structure. Polyether defoamers are often used in systems where compatibility with the foaming medium is crucial. For example, in the detergent industry, polyether defoamers are added to control foam during the washing process, as they can work well in the presence of other surfactants and additives in the detergent formulation.
Applications of Defoamers
- Food and Beverage Industry
-
- In the food and beverage industry, defoamers are used to control foam during various production processes. For example, in the brewing of beer, foam control is essential. Excessive foam during the fermentation process can cause overflow and loss of product. Defoamers are added in carefully controlled amounts to ensure that the fermentation proceeds smoothly without affecting the taste and quality of the final product. In the production of fruit juices, defoamers are used to remove foam that may form during the extraction and concentration processes.
- Chemical Industry
-
- In chemical manufacturing, defoamers are used in a wide range of processes. In the production of polymers, such as polyethylene and polypropylene, foam can form during the polymerization reaction. Defoamers help to maintain a stable reaction environment, prevent reactor fouling, and ensure the quality of the polymer product. In the petrochemical industry, during oil refining processes, defoamers are used to control foam in distillation columns and other processing units.
- Paper and Pulp Industry
-
- In the paper and pulp industry, defoamers are used to eliminate foam in the pulp suspension. Foam in the pulp can cause problems such as uneven paper formation and poor paper quality. Defoamers are added to the pulp slurry to break down the foam, allowing for a more efficient papermaking process. This results in a smoother and more uniform paper product.
Conclusion
Defoamers are essential additives in numerous industries. Their ability to control foam effectively improves production efficiency, product quality, and equipment performance. As industries continue to develop and demand more efficient and environmentally – friendly solutions, the research and development of defoamers will also progress. New types of defoamers with improved performance, better compatibility, and reduced environmental impact are expected to emerge in the future, further enhancing their applications across various sectors.
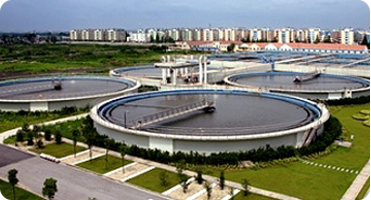